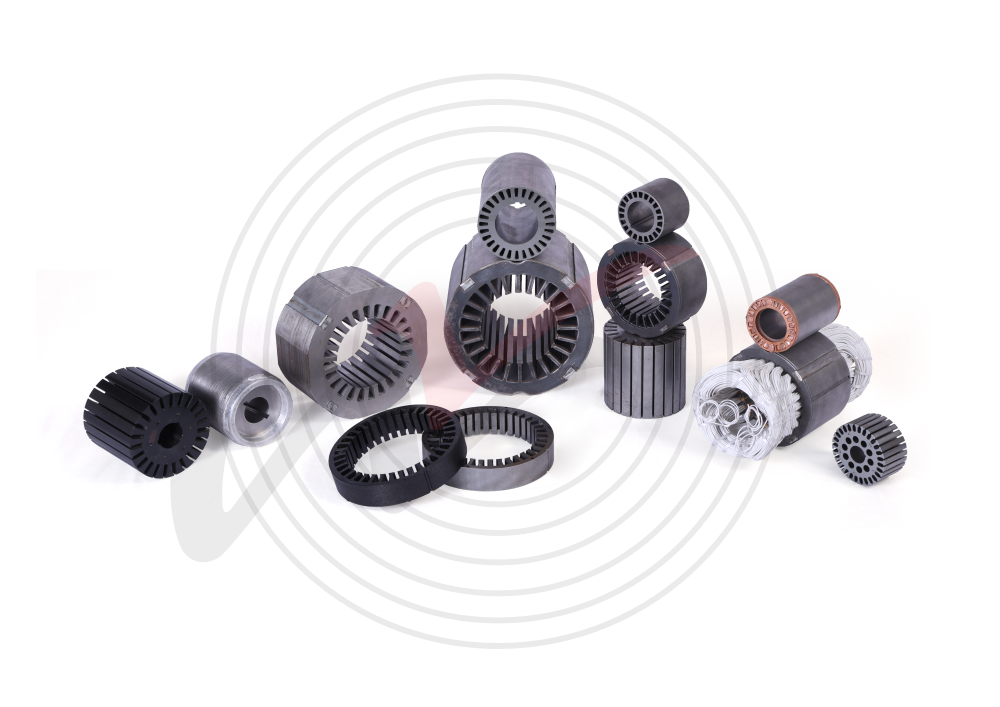
Electrical Stamping And Lamination
Since 1996 Vipul Copper has been involved in the R&D and manufacturing of high-quality complex iron core motor laminations and lamination stacks. Our focus is the manufacture of motor laminations and lamination stacks for stators and rotor cores for submersible motors, tubular motors, home appliance motors, elevator motors etc.
Our robust tooling offers a low cost alternative to manufacturers with moderate to high volume lamination requirements. Our average lead time on tooling for lamination and lamination stacks ranges from 10-12 weeks. Carbide tooling is also an option with almost the same lead time as typical tool steel dies. In addition, with press capabilities of over 250 strokes per minute, and up to 250tons of force, our prices are very competitive. As a custom lamination manufacturer, we can supply custom motor laminations and lam stacks in all shapes and sizes. Our toolmakers are able to build and maintain a wide variety of production dies. Our stamping presses can accommodate dies with a maximum length of 1800mm. We have the capacity to process 3000 tons of silicon steel sheet into motor laminations annually.
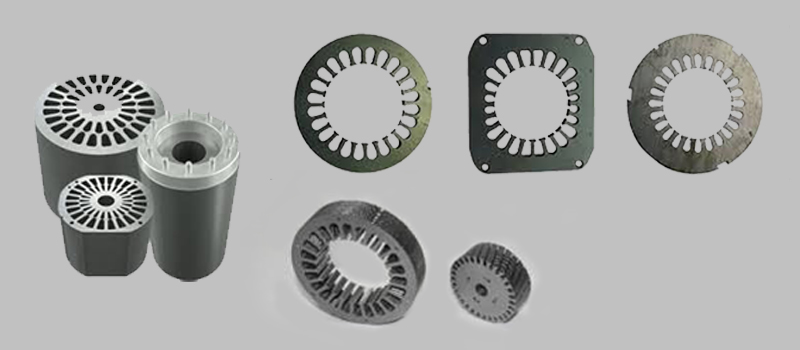
- Rotor Laminations
- Stator Laminations
- Welding Laminations
- Armature Laminations
- Transformer Laminations
- Custom Laminations
- Stake Core Laminations
- Progressive Dies
- Compound Dies
- Progressive Staking Dies
- Semi-Processed and Fully Processed Silicon Steel
- Cold Rolled Motor Lamination Stee
- Annealing
- Stress Relief Annealing
- Stacking and welding
Vipul ensures excellent quality custom motor laminations and lamination and is very price competitive in Cold Rolled Motor Lam Steel, Silicon Steel, . Vipul has audited, qualified and worked with QS-9000 and ISO certified lamination factories in India.
LAMINATION TUTORIAL
Few decisions in the design of an electric motor are as fundamental, or have as far reaching consequences as the selection of the material to be used in the rotor or stator motor laminations, which become lamination stacks. Motor output, heat rise, weight, and cost are only a few of the characteristics which are profoundly influenced by the selection of core material. ( The term motor is used loosely here to include generators, tachometers, resolvers, alternators, etc).
No one material is optimum (or even usable) for every application. As with all design decisions, trade offs must be made between cost, weight, size, and other factors. In addition, the processing of the laminations after fabrication can have a large influence on the performance of the unit being designed.
The criteria for material selection include cost, permeability, core losses, and saturation flux density. Permeability and core losses vary with the frequency of flux reversals (in Hz), and with flux density. In certain applications, the shape of the hysteresis curve becomes important. Each of the available materials is optimized for one or more of these properties, while being less than perfect in other areas. Custom laminations and custom lam stacks are often required.
Cold Rolled Motor Lam Steel (CRMLS)
Also called Cold Rolled Lamination Steel, this material is the lowest cost material for volume applications. In terms of tonnage, this is probably the most common material in use today. Ease of stamping and low tool wear help to contribute to the low cost of finished laminations. Carbon steel should be considered for applications where relatively high core losses are acceptable (D.C. pole pieces, low duty cycles, etc.) and low first cost of the end unit is of primary importance. This material is almost always annealed after stamping to develop optimum properties. This adds little to the cost when done in a continuous furnace, and allows an oxide coat to be added to the surface to provide interlaminar resistance. The heat treatment is somewhat critical, and the supplier should be consulted prior to specifying an annealing cycle. When properly annealed, modern grades of Lamination Steel have core losses rivaling the lower grades of silicon steel.
Silicon Steel (Electrical Steel)
When low carbon steel is alloyed with small quantities of silicon, the added volume resistivity helps to reduce eddy current losses in the core. Silicon steels are probably of the most use to designers of motion control products where the additional cost is justified by the increased performance. These steels are available in an array of grades and thicknesses so that the material may be tailored for various applications. The added silicon has a marked impact on the life of stamping tooling, and the surface insulation selected also affects die life. Silicon steels are generally specified and selected on the basis of allowable core loss in watts/lb.